
Are Kanban Boards applicable to all industries?
Tune in and get Inspired 🎧
Getting your Trinity Audio player ready...
|
What does Kanban mean?
A Kanban Board is a system that signals the need for action in the business world. It’s a Japanese word that means “card” or “signal.” The Kanban method was first developed by Taiichi Ohno, an industrial engineer at Toyota, in the 1950s to streamline production and eliminate waste.
The Toyota Production System utilizes a “Kanban” board to help organize and streamline the production process. This system is designed to help keep production moving smoothly and efficiently by visualizing the workflow.
Estimated reading time: 14 minutes
Table of contents
- What does Kanban mean?
- What is a Kanban Board?
- What is an example of Kanban?
- How do Kanban practices help businesses?
- Kanban Boards in the Manufacturing Process
- What are the benefits of using the Kanban system?
- What is the main objective of the Kanban method?
- What is a Kanban board used for?
- How does Kanban work?
- Who manages the Kanban Board?
- What is a scrum master?
- What are the five practices in Kanban?
- What are some examples of industries that could use Kanban?
- Is Kanban a Lean Methodology or Agile?
- Conclusion
The Kanban Board helps Toyota track production lines running like a well-oiled machine by clearly seeing what needs to be done and where bottlenecks occur.
What is a Kanban Board?
Digital Kanban Boards or physical Kanban Boards help to visualize and manage work flowing through a system. It does this by showing the status of each task, who is working on it, and where it is in the process. This makes it an essential tool for managing work, from simple to-do lists to complex projects.
Kanban Boards are popular in software development but can be used in any industry where work needs to be managed. For example, they can be used in manufacturing to track the progress of products through the assembly line or in healthcare to track patients as they move through the system.
There are many Kanban Boards, but they all share the same basic features. Each board has a space for each task, and each task has a status. The most common statuses are “to do,” “in progress,” and “done.”
The Kanban Board is designed to encourage acts of leadership at all levels. It does this by making the process explicit and providing feedback loops. This enables people to take responsibility for their work and to manage the flow of work through the system.
The Kanban Board is also a scheduling system. This means that it can be used to plan when tasks should be started and finished. Kanban Boards are not a replacement for the scientific method, but they can help manage the flow of work. Visualizing the workflow makes it easier to identify bottlenecks and optimize the process.
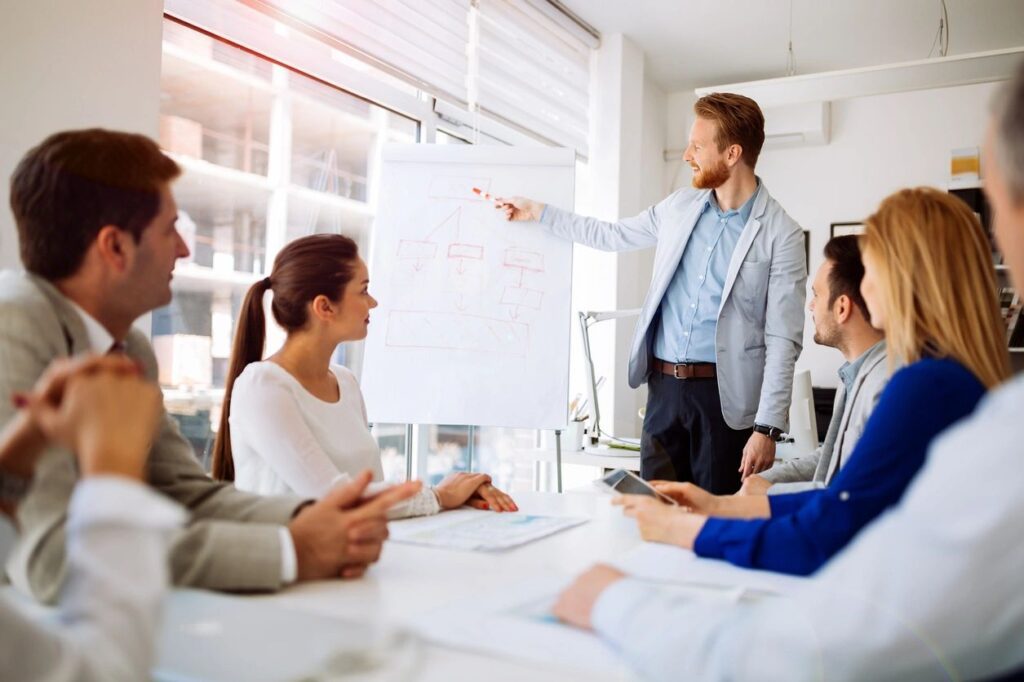
Many different metrics can be used to measure the performance of a Kanban Board. The most common metric is cycle time, the time it takes for a task to move from the “to do” status to the “done” status. Other important metrics include lead time, throughput, and work in progress.
The time it takes for a work task to move from the “to do” status to the “in progress” status is considered lead time. The number of tasks completed in a given period is the throughput, and work in progress is the number of “in progress” tasks at any given time.
These metrics are essential, but cycle time is the most important. This is because it is the best measure of how well the Kanban Board works. If the cycle time is extended, then it means that tasks are taking too long to complete. Kanban Boards have been known to help with these issues by visualizing blocked tasks, poor estimation, or lacking resources for tasks and progress.
Kanban Boards are a great way to improve the flow of work, but they’re not a silver bullet. They can be a valuable tool in your arsenal, but they won’t solve all your problems.
What is an example of Kanban?
Kanban typically consists of physical boards with three columns: To Do, In Progress, and Done. Each column represents a stage in the process, and as tasks are completed, they are moved from one column to the next.
The Kanban method is designed to visualize workflow and limit the amount of Work In Progress (WIP). This helps to prevent bottlenecks and ensure that work is completed promptly.
Kanban can be applied to any industry or business. For example, a software development team may use a Kanban board to track the progress of their project. A sticky note or Kanban card contains the task description in the board’s appropriate column. The team may set limits on the number of tasks that can be In Progress at any given time. This helps to prevent bottlenecks and ensure that work is completed promptly.
The Kanban method is based on the following values: transparency, collaboration, respect, and continuous improvement. These values help to improve communication and workflow within an organization.
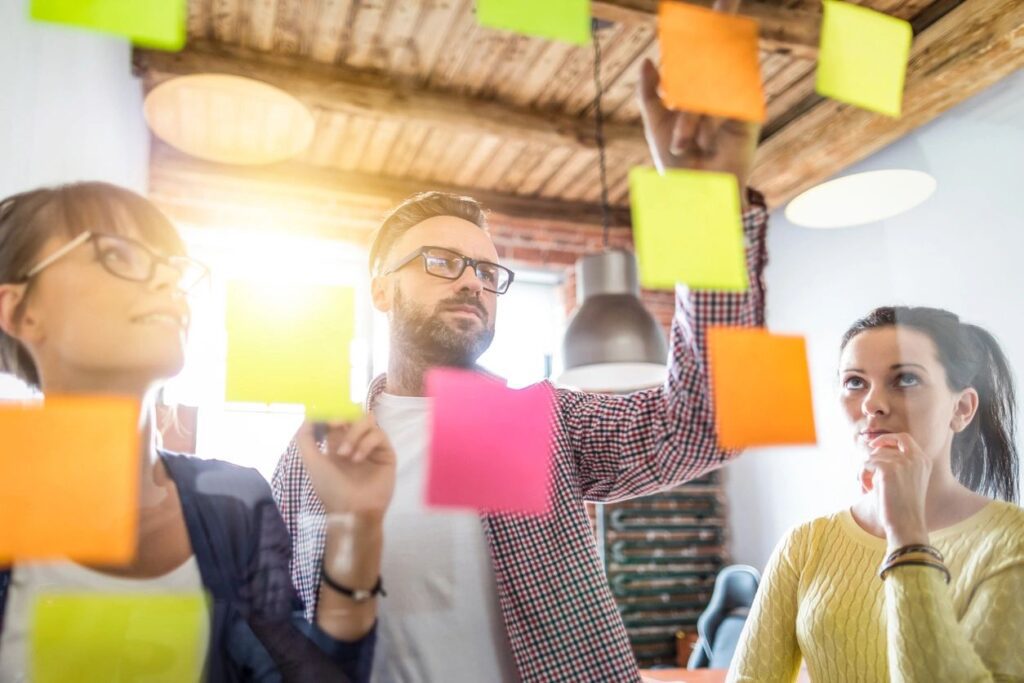
How do Kanban practices help businesses?
By adopting Kanban, businesses can improve their operations in several ways, including:
Reducing waste:
By visualizing workflow, Kanban can help businesses identify areas with unnecessary WIP or inefficient processes. This can help to reduce waste and improve quality.
Improving communication:
The Kanban method can help improve communication between team members by clarifying who is responsible for each task.
Enhancing collaboration:
Kanban can also enhance collaboration by providing transparency into the work process and allowing team members to see the progress of others.
Increasing efficiency:
WIP limits and maximizing transparency, Kanban can help businesses to increase their overall efficiency.
Kanban Boards in the Manufacturing Process
Businesses have since adopted the Kanban method in a variety of industries as a way to improve efficiency and quality. Kanban Boards can be used in any industry to help improve business processes. Businesses can maximize efficiency and throughput by visualizing workflows and setting limits on work in progress. Kanban can be adapted to any industry and is not limited to the manufacturing process or software development.
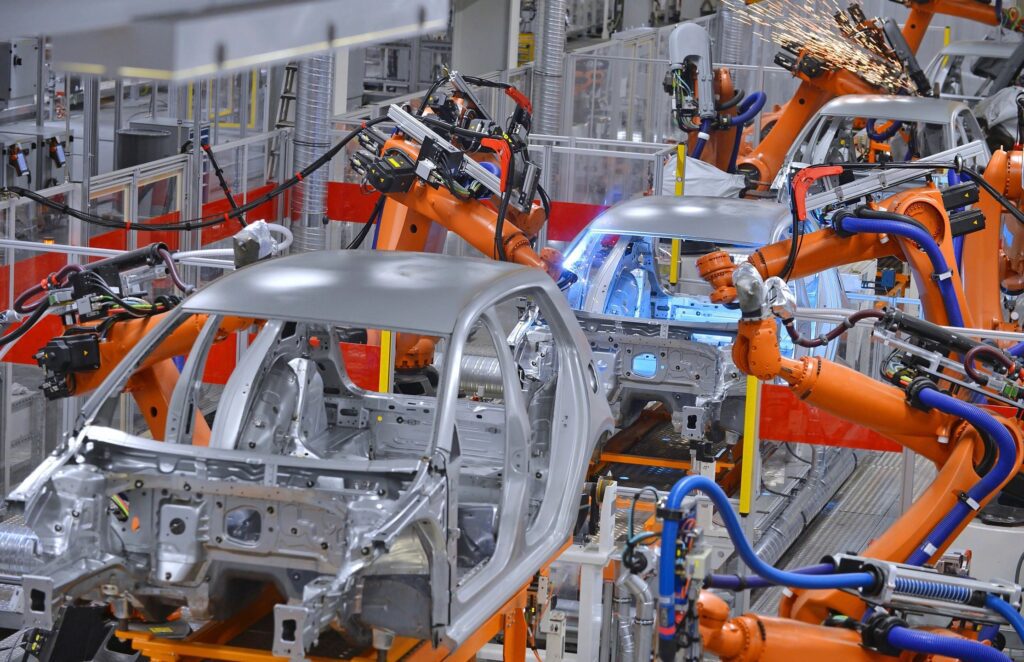
What are the benefits of using the Kanban system?
The Kanban system is a tool that can be used to help businesses in a variety of industries improve their operations. By minimizing waste, improving communication, and maximizing transparency, companies using Kanban can improve product and service quality, increase efficiency, and enhance collaboration. These benefits can lead to improved customer satisfaction.
Kanban can be used to help businesses in a variety of industries improve their operations. Recently, Kanban has become increasingly popular for managing work flow and improving productivity. The principles of Kanban are based on continuous improvement, or “kaizen.” This philosophy emphasizes the need for businesses to constantly strive to improve their products, services, and processes.
The Kanban system is built around the idea of “flow.” Flow is the continuous movement of work from one stage to the next in a process. Kanban aims to help businesses improve their flow by identifying bottlenecks and eliminating them.
A vital advantage of the Kanban is that it encourages businesses to make small, incremental changes rather than large, sweeping changes. This “evolutionary” approach to change is often more successful than revolutionary change because it is less disruptive and easier to implement.
Another advantage of Kanban is that it helps businesses to visualize their work flow. By using digital kanban boards, companies can track the progress of work items as they move through the various process stages. This visibility can help identify bottlenecks and other problems to be corrected.
The Kanban system is founded on values emphasizing collaboration, respect, and continuous improvement. These values can help to create a more positive and productive work environment.
While Kanban is not appropriate for all businesses, it can be very effective for those willing to adopt its principles. When used correctly, the Kanban system can help companies to improve their operations, reduce waste, and increase productivity.
What is the main objective of the Kanban method?
The main objective of the Kanban methodology is to help businesses improve their efficiency and quality by minimizing waste and maximizing transparency. In addition, Kanban can also help to enhance collaboration among team members. Ultimately, these objectives can lead to improved customer satisfaction.
What is a Kanban board used for?
Kanban physical boards are used as a tool to visualize work and track the progress of tasks. It is typically divided into three columns: To Do, In Progress, and Done. As tasks are completed, they are moved from one column to the next.
The Kanban approach is designed to help businesses improve their efficiency and quality by minimizing waste and maximizing transparency. In addition, Kanban can also help to enhance collaboration among team members. Ultimately, these objectives can lead to improved customer satisfaction.
How does Kanban work?
Kanban is a system for continuous improvement that was initially developed for use in manufacturing. However, it can be applied to any industry or process. The basic principle is to create a digital Kanban Board or a physical Kanban Board with columns for each process stage.
Cards or sticky notes are then used to represent tasks. These tasks are moved from column to column as they are completed. Working closely with the development team, the scrum master ensures a smooth work flow, potential blockers are removed, and tasks are not started until they are ready, which is the commitment point.
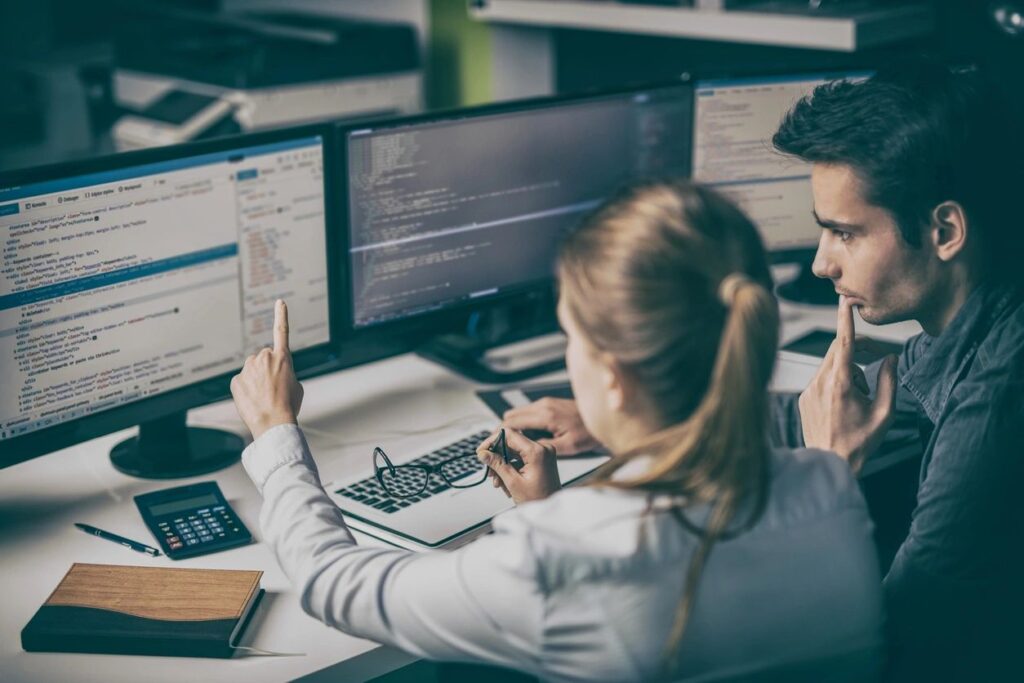
Kanban is used in manufacturing, product launches, project management, and many other industries. These flexible Kanban systems can be customized to fit the needs of any organization. Kanban can be used with scrum or as a standalone system.
A service request manager can use Kanban to manage the flow of work and visualize progress. Kanban cards can represent tasks, which can be moved from column to column as completed. This explicit implement feedback loops system encourages teams to work together so that potential blockers can be removed and improvements can be made.
Remote teams can benefit from using Kanban to manage their work, as it is a visual management system that can track progress and limit work in progress. The whole team can be involved in managing the Kanban process, which helps to ensure that everyone is aware of the work that needs to be done and the status of each task.
Who manages the Kanban Board?
Write a paragraph and use the following key terms, physical kanban board, kanban system, electronic kanban systems, kanban cards, sticky notes, service delivery manager, kanban principles, kanban encourages managing flow, flow metrics, managing flow, scrum board.
Kanban Boards apply to software development or IT industries and all other industries. It is a physical board where sticky notes with written tasks are placed and moved as the tasks get completed. The board is divided into different columns that signify the task’s progress.
For instance, the first column could be “To Do,” the second column could be “In Progress,” and the last column could be “Done.” There are also electronic Kanban Boards that are used to manage tasks electronically.
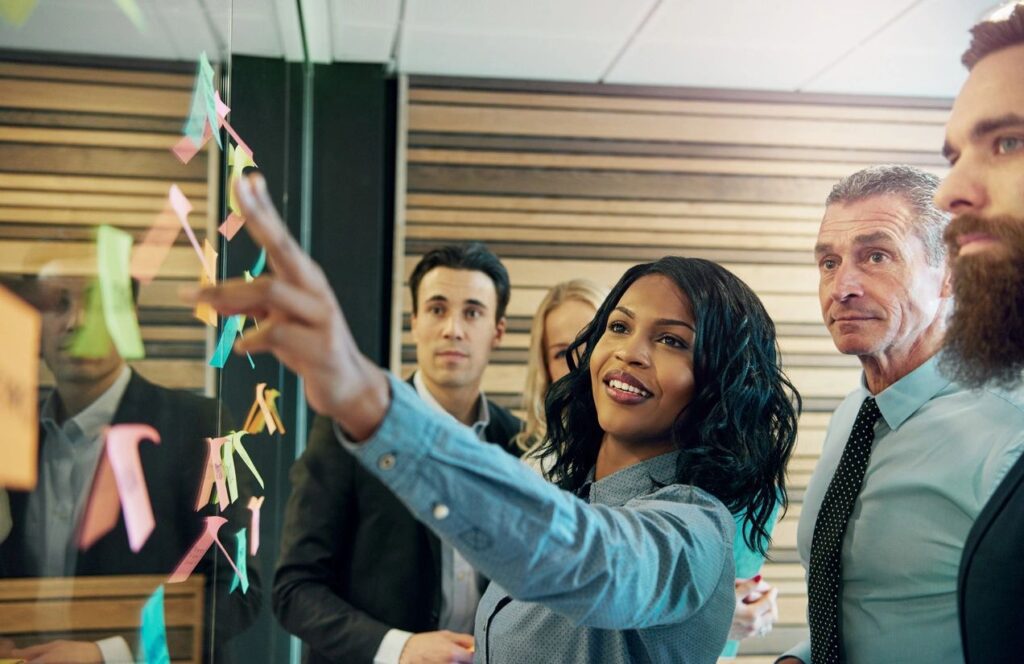
Reviewing the backlog items using a physical Kanban Board.
In such a system, Kanban cards are used to represent tasks, and these cards are moved across different columns on the board as the task progresses. The Kanban Board is managed by the Service Delivery Manager, and the Kanban principles are followed to ensure that the flow of work is smooth.
The Kanban Board encourages collaboration and transparency among team members and helps manage flow metrics.
Managing flow is essential in any industry as it helps achieve better results and meet deadlines. The scrum board is another tool that can be used for managing flow. It is similar to the Kanban Board but is more suited for agile software development.
It helps track the progress of tasks and provides a visual representation of the work that has been completed.
What is a scrum master?
A Scrum Master is a job title within the software development industry. The role of a Scrum Master is to help a team of developers to work together more effectively, and to improve the quality of their output. A Scrum Master is not a traditional project manager; they are more like a facilitator or coach, and their primary concern is with the process of software development, rather than with individual tasks.
Kanban Boards are a tool that can be used to help manage and improve the flow of work in any industry, not just software application development. They are particularly well suited to industries where knowledge work is essential, such as service request management or service delivery management.
Making Kanban Boards work well is to make the process policies explicit. This means clearly understanding the job titles and roles involved and the metrics that will be used to measure success. Without this clarity, it can be challenging to know who’s responsible for what and how progress should be measured.
What are the five practices in Kanban?
The five core practices in Kanban are:
Visualize workflow: Kanban Boards help businesses visualize work and track the progress of tasks. This can help to identify areas with unnecessary WIP or inefficient processes.
- Limit WIP: The Kanban method helps businesses limit work in the amount of WIP items. This can prevent bottlenecks and ensure that work is completed promptly.
- Enhance collaboration: Kanban can also enhance collaboration by providing transparency into the work process and allowing team members to see the Progress of others.
- Set completion dates: To keep work flowing smoothly, it is essential to set completion dates for each task. This will help to ensure that deadlines are met, and that work is not left unfinished.
- Measure and review progress: It is also essential to measure and review progress regularly. This can help businesses identify areas where Kanban works well and areas for improvement.
- Improvements: The final step is to make improvements based on the findings from the previous step. This can help businesses continuously improve their efficiency and quality.
What are some examples of industries that could use Kanban?
Kanban can be used in any industry where there is a need to improve efficiency and quality. Some examples of initiatives that could use Kanban include:
- Manufacturing – To improve production, kanban boards can be used to track the progress of individual products through the manufacturing process.
- Software development – Kanban is prevalent in software development because it helps developers visualize their progress and minimizes the amount of work in progress (WIP).
- Healthcare – Kanban can help healthcare professionals track patients’ medical history, test results, and other important information.
- Banking and Finance – Banks can use kanban boards to track customer inquiries, account openings, and other banking tasks.
- Government – Governments can use kanban boards to track budget allocations, tax payments, and other financial operations.
- Education – Teachers can use kanban boards to keep track of student assignments, grades, attendance records, and other essential data.
- Retail – Retailers can use kanban boards to keep track of inventory levels, sales data, shipping times, and other important information.
Is Kanban a Lean Methodology or Agile?
Kanban is often considered to be part of the Lean methodology. This is because both approaches aim to help businesses improve their efficiency and quality by minimizing waste and maximizing transparency.
In addition, both Kanban and Lean emphasize the importance of continuous improvement. Kanban is not limited to Lean or Agile teams and organizations – it can be used in any business.
Kanban can be used in any business as it is not limited to just Lean or Agile teams and organizations. The entire process can be seen, and transparency is improved, which helps to reduce waste and increase efficiency.
Successful implementation of Kanban can help to improve the current processes by identifying areas where there is excess inventory or where the flow is not managed effectively.
The board represents the inventory system and helps to manage the flow of work efficiently. This allows businesses to focus on continuous improvement, leading to increased quality and profitability.
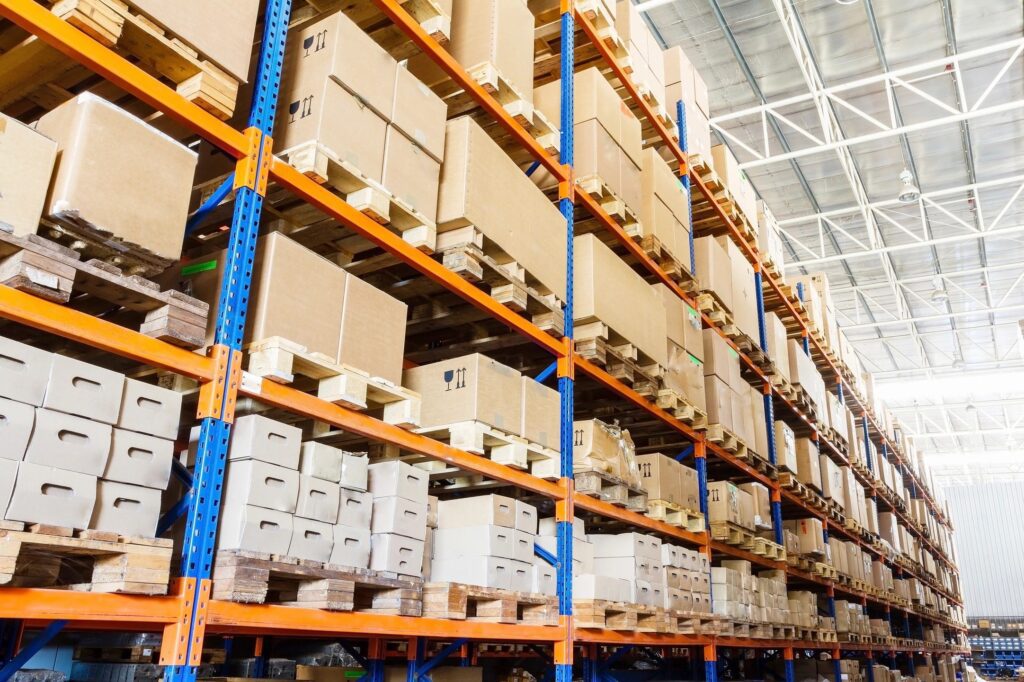
Conclusion
Kanban Boards are a great way to improve efficiency and quality in any industry. Businesses can optimize their processes by visualizing workflows and setting limits on work in progress. If you’re interested in learning more about how Kanban can be used in your industry, mediaTCgroup can help. We specialize in using this approach to reach business goals across industries. Contact us today to learn more about our services!
Don’t miss out on opportunities to improve your business efficiency – contact mediaTCgroup today and see what we can do for you!
If you are new to our website, we would like to welcome you. Consider subscribing to our blog/newsletter to access exclusive content and discounts on our online shop.